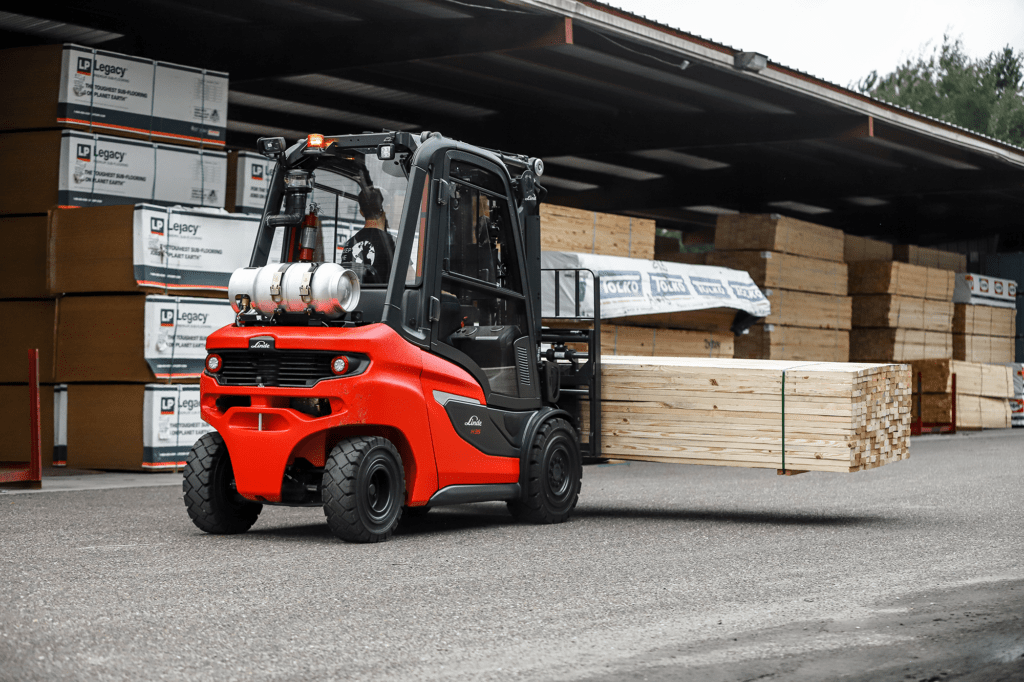
Linde Material Handling
North America
Latest Posts
- Protected: Delivering Hope in the Aftermath of Hurricane HeleneThis content is password protected.
- Protected: Through a Caregiver’s Eyes: Navigating Life After a Breast Cancer DiagnosisThis content is password protected.
- The Faces of KION North America: Employee of the Quarter: Kevin Crawford, Quality Operations EngineerMeet Kevin Crawford, a dedicated professional at KION NA whose journey over the past four years has been marked by remarkable accomplishments and a steadfast commitment to continuous improvement. In this exclusive interview, Kevin shares his …
Featured Categories
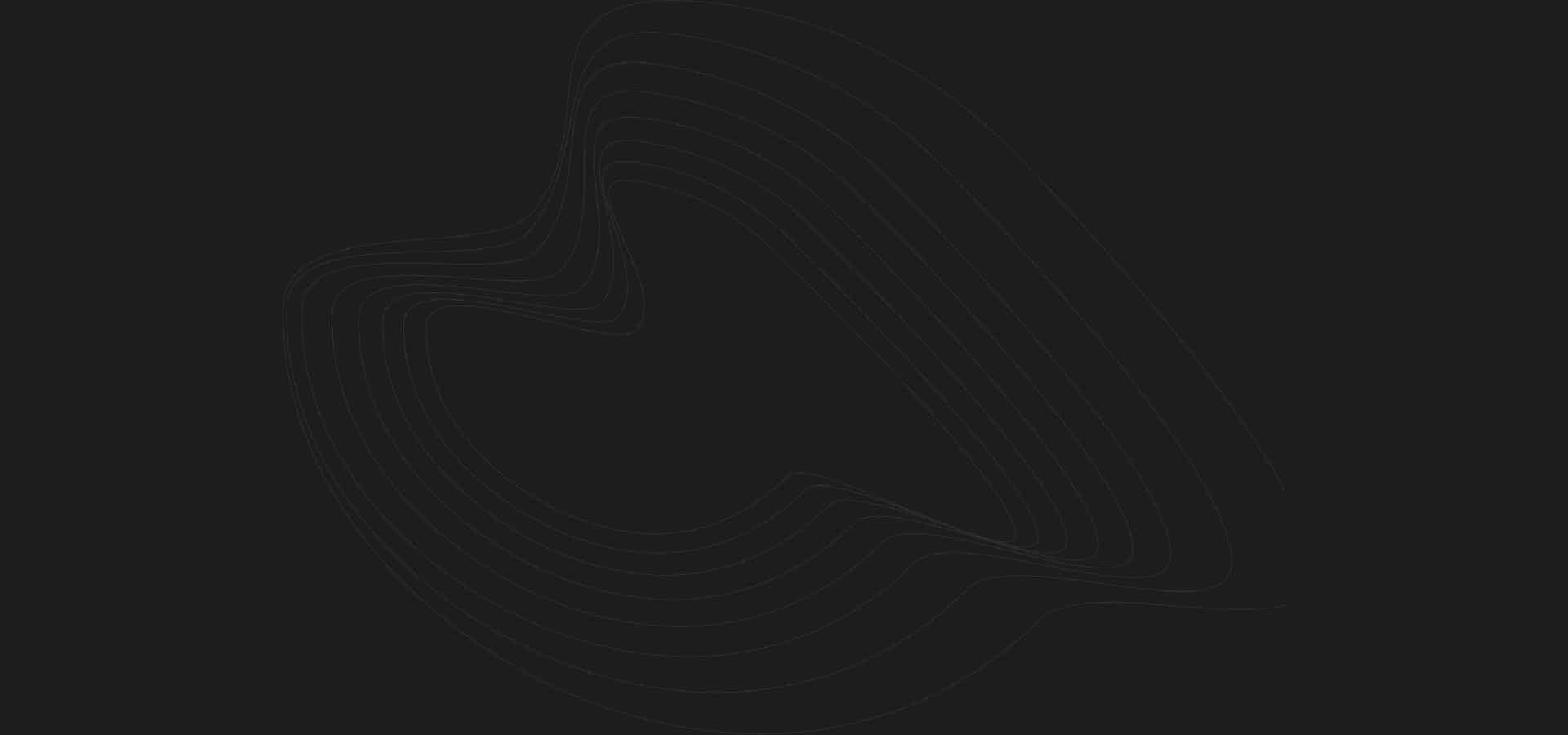
Sign up for product updates and the latest news from KION NA!
You have the right to revoke your subscription to the newsletter at anytime.
Get the Equipment You Need
Linde Forklift Dealers Throughout North America
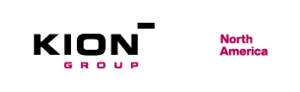
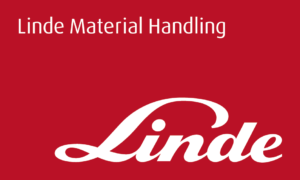
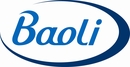
“Linde lifts have been an excellent addition to our company since 2001. We have experienced greater productivity with Linde lifts. With great productivity, we have had greater efficiency and lower operating costs as well as lower manpower costs. The bottom line is that we handle more lumber with less lifts and less people by using Linde“ – Richard, Southeast Wood Treating, Ltd.
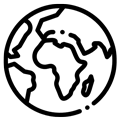
TRUSTED WORLDWIDE – SERVING NORTH AMERICA
Easily find and contact your local material handling equipment dealer with our convenient Find a Dealer tool. Questions? Contact us!