Table of Contents
Updated: 8/16/2021
When it comes to running a productive and efficient warehouse, safety should be your first priority. But because the profit behind safety efforts is not easy to quantify directly, organizations sometimes put those efforts on the back burner. However, a safe warehouse puts companies in a position to be more profitable and generate cost savings. Additionally, an unfortunate workplace accident or injury can have highly detrimental consequences on a warehouse and hinder its efficiency.
With the proper steps in place, you can avoid accidents and their costly consequences and see better profit over the long haul.
Creating a Warehouse Safety Checklist
There are many safety hazards in a warehouse that can be dangerous if not properly addressed. Having a safety checklist is a great way to identify any potential risks in the workplace. Once those hazards are identified, they can be dealt with to prevent any harmful incidents and maintain a safe work environment. There are many aspects of warehouse safety to consider, from handling materials correctly to electrical and employee safety.
General Warehouse Safety
When it comes to general warehouse safety, there are easily preventable hazards resulting in injury if not addressed beforehand. Therefore, some items on your checklist should include:
- Loading Docks: Exposed or open loading docks are blocked or roped off, as well as any other areas where employees could potentially fall four feet or more.
- Floor Debris: Keep warehouse floors clear of debris, garbage, and all obstacles. Maintain clear aisles at all times. Floors should be clear of anything that can pose a potential risk; this includes extension cords, loose wires, trash, hoses, for example. These items can cause harm and potential danger to the machines and also employees.
- Ventilation: The warehouse is well ventilated.
- Keep the Warehouse Organized: For workers to move safely through the space, your warehouse must be organized. A well-organized space will make it easier for workers to move about safely and improve efficiency and productivity. Your warehouse and its aisles should be free of clutter, electrical cords, or other potentially hazardous materials that could result in a fall or other injuries.
- Floor Damage: Inspect often for floor damage and rack damage; repair immediately. Uneven, rough floors that are not paved or smooth can damage machine tires. Tire damage can prevent operators from properly loading and unloading equipment or cause materials to fall off the machines and cause further damage.
- Crash Barriers: Use crash barriers and pedestrian barriers on the production floor. Crash barriers help to create traffic lanes specifically for the machinery and act as a barrier between the machines and the workers. The pedestrian barriers do the same as the crash barrier by preventing forklifts from contacting employees. Crash barriers, pedestrian barriers, and guard rails are provided to protect employees from interacting with forklifts and other machinery. These barriers keep machines in their traffic areas to prevent collisions.
- Use Proper Warning Signage: Clearly label hazardous zones and proper signage throughout the warehouse. Good signage throughout the facility is a great way to inform employees about potential hazards. All dangerous materials need to be appropriately labeled and identified, and loading zones should be marked and sectioned off.
- Inspect Work Stations: Ensure that workstations are being kept clean and free of litter. Accumulation of debris can cause falls, trips, chemical spills and jeopardize someone’s safety. Implement better cleaning standards for all your employees to follow to avoid these potential risks.
Material Handling Safety Checklist
Essential items to include on your checklist to ensure the safe handling of materials includes:
- Safe clearance for equipment and materials through aisles and doorways.
- Motorized vehicles or mechanized equipment are checked daily or before use.
- Vehicles are shut off, and the brakes are set before loading/unloading.
- Securing chains, ropes, slings are adequate for the required job to be performed.
- Covers and guardrails have been provided to protect workers from stair openings in floors, equipment pits, and other hazards.
- Constantly have maintenance checks on forklifts and other machinery for repairs, damages, and updates. In addition, newer versions of forklifts are equipped with safety features that alert operators on battery life and needed repairs. Constant inspection of these safety features will keep injury rates low.
Employee Safety
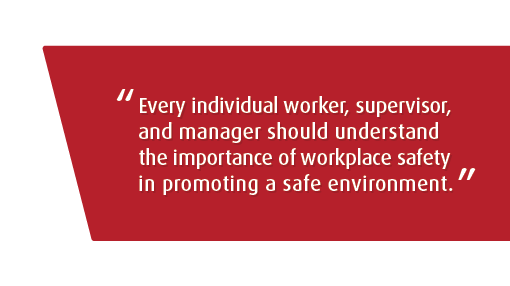
A warehouse can pose many health and risk factors to its workers if the correct safety procedures and standards are not in place. When lifting and handling heavy materials in the warehouse, these factors can lead to severe injury and even chronic conditions or disability. Not only do such injuries decrease warehouse efficiency, but they can also cost the organization a substantial amount in worker’s compensation and disability insurance.
Every individual worker, supervisor, and manager should understand the importance of workplace safety in promoting a safe environment. The following tactics can help to create a culture of safety in your warehouse operation:
- Work Schedules: Employees performing physical work are given adequate time for rest breaks to avoid fatigue.
- Environment Training: Employees are trained to safely work in the environment (hot/humid or cold).
- Daily Expectations: Set reasonable deadlines for employees to avoid time pressures that may lead to unsafe practices or substandard work that can cause any accidents. Extreme time pressure can cause more harm than good to companies. Overworking employees and creating stressful environments can lead to physical stress, less productivity, and serious injuries.
- Institute Safety Education and Training: It’s imperative to fully train and educate employees about your warehouse’s safety requirements and procedures, and these policies should be revisited over time. If new safety procedures or systems are introduced to the workplace, further education and training should occur due to new equipment or organizational method.
- Ongoing Learning: Recertify your forklift operators with updated training every three years per OSHA guidelines. Have panels, meetings, and training to discuss more effective and safer practices for forklift operators every year. An effective way to minimize potential forklift-related injuries is to train and evaluate all forklift operators constantly. Those who know how to properly handle and operate forklifts, combined with town hall meetings, will ensure that operators follow safety procedures and reduce risks.
- PPE Supply and Use: Ensure that PPE and other safety equipment are being used at all times while on the production floor and in the warehouse. PPE is essential when it comes to handling equipment or other hazardous material. Equipment such as hard hats, special glasses, and gloves are appropriate personal protective equipment to use when handling dangerous materials.
Reduce Ergonomic Risks Factors
While many aspects of the warehouse environment fall under worker safety, from forklift safety to proper training, ergonomics refers to those injuries to the musculoskeletal system, often sustained from forceful exertion, sustained awkward postures, repetitive motions, and more.
One great way to spot ergonomic risks is to walk through the warehouse and observe workers perform their daily tasks. Take care to notice any awkward or strained positions or note that specific tasks are causing employees considerable discomfort. If you discover ergonomic risks, the next step is to work to control and reduce those risks.
OSHA recommends three areas of control for ergonomic hazards:
- Engineering controls: Engineering controls refer to a physical change in the working environment. This change may include installing a mechanical device to help with heavy lifting or reducing the weight of a specific load to prevent overexertion.
- Administrative and work practice controls: This involves redesigning warehouse processes and procedures. Management may implement more breaks or require multiple people to lift loads over a certain weight.
- Personal protective equipment: Workers must be equipped with the proper personal protection to reduce risk.
Finally, a vital aspect of ergonomic safety in the warehouse is to listen to your employees. If a worker comes to you expressing concerns about conditions or discomfort performing a particular task, do not write them off. Instead, listen and discuss these issues with your workers and find ways to solve any existing problems or ease discomfort. The more comfortable and safe workers are, the more productive the warehouse will be.
Electrical Safety for Warehouse Applications
Electrical safety is a significant part of the overall safety of the warehouse. The factory floor is full of electrical tools and cords that can pose a severe hazard when not dealt with safely. There are many essential safety steps to take when it comes to electrical equipment, exposed wires, grounding, and more:
- Equipment Grounding: Properly grounding electronic equipment will decrease the likelihood of someone being shocked. Be sure power cords are not blocking work aisles or paths, leading to employee falls and injuries.
- Ongoing Inspection: Employees are instructed to perform preliminary inspections and appropriate tests before beginning work on electrical equipment or lines.
- Portables: Portable electric equipment and tools are either grounded or double insulated.
- Damage: Exposed wiring or cords with frayed or damaged insulation are repaired or replaced immediately. Outlets should also be in prime condition, with no exposed wiring or other damage. Flexible cords and cables are free of splices and taps.
- Exposure to Conductors: Be sure to keep all electrical equipment away from any wetness. The area surrounding electrical cords and equipment should be free of any potentially hazardous materials or conductors, such as water or metal.
- Employee Training: Employees who regularly work around energized electrical equipment or lines are instructed in CPR methods. Teach proper use of tools, alert workers to the possible hazards of working with electrical equipment, and show them where circuit breakers and electrical panels are located.
While these guidelines are essential in the beginning to create your warehouse safety checklist, they are just the tip of the safety iceberg. The Occupational Safety and Health Administration has some great guidelines and templates for general warehouse safety and specific safety concerns, such as fire safety, floor and wall openings safety, and much more.
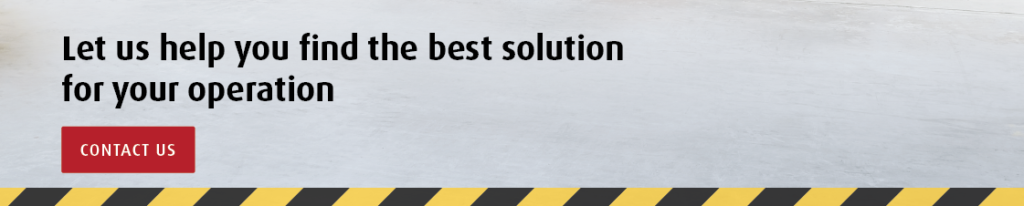
At Linde Material Handling we understand the importance of warehouse safety and ensuring your team has the right equipment for daily operations. Contact us or find your local lift truck dealer for more information on our solutions.