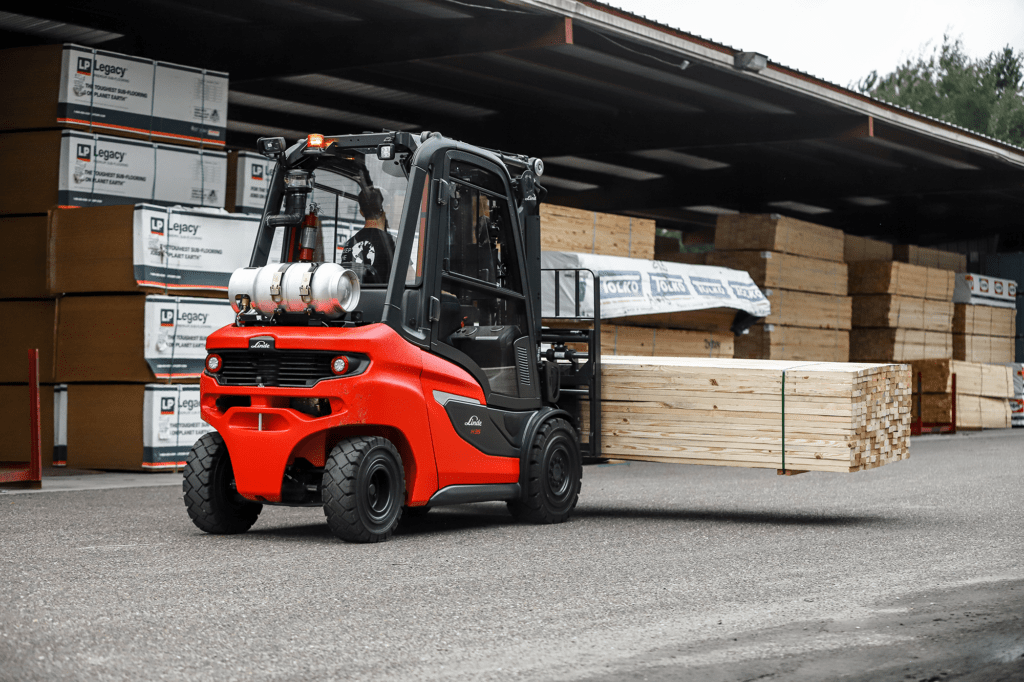
Linde Material Handling
North America
Latest Posts
- The Faces of KION North America: Employee of the Quarter: Joseph Moore, Team Lead, WeldWelcome to our latest installment of the Faces of KNA: Special Edition. In this issue, we have the privilege of sitting down with Joseph Moore, the esteemed winner of the Employee of the Quarter award and …
The Faces of KION North America: Employee of the Quarter: Joseph Moore, Team Lead, Weld Read More »
- Your Essential Spring Forklift Maintenance Checklist for Efficient and Secure OperationsAs spring arrives, it’s prime time for a thorough check-up on your forklift trucks. In environments with seasonal changes and temperature fluctuations, ensuring the functionality of your equipment is paramount for smooth operations. Follow this guide …
Your Essential Spring Forklift Maintenance Checklist for Efficient and Secure Operations Read More »
- Powering Productivity: The Linde T20 Series 1151 Electric Pallet TruckIn the fast-paced logistics and material handling world, having equipment that embodies efficiency, performance, and confidence is essential. Enter the Linde T20 Series 1151 Pallet Truck, a powerhouse among Class 3 offerings engineered to tackle the …
Powering Productivity: The Linde T20 Series 1151 Electric Pallet Truck Read More »
Featured Categories
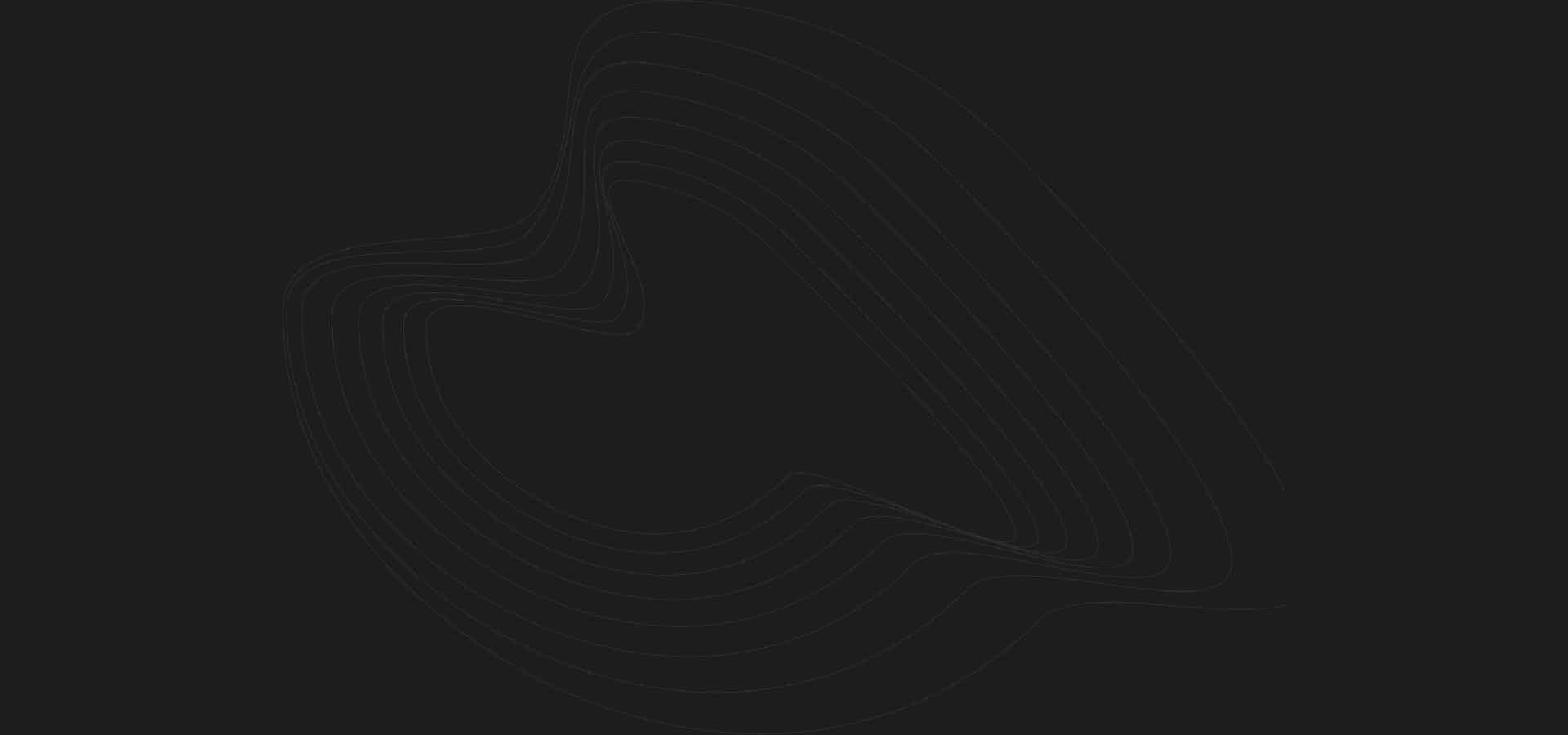
Sign up for product updates and the latest news from KION NA!
You have the right to revoke your subscription to the newsletter at anytime.
Get the Equipment You Need
Linde Forklift Dealers Throughout North America
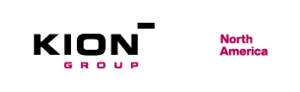
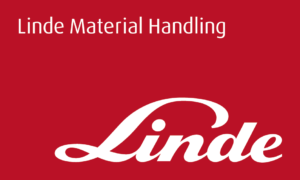
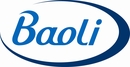
“Linde lifts have been an excellent addition to our company since 2001. We have experienced greater productivity with Linde lifts. With great productivity, we have had greater efficiency and lower operating costs as well as lower manpower costs. The bottom line is that we handle more lumber with less lifts and less people by using Linde“ – Richard, Southeast Wood Treating, Ltd.
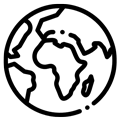
TRUSTED WORLDWIDE – SERVING NORTH AMERICA
Easily find and contact your local material handling equipment dealer with our convenient Find a Dealer tool. Questions? Contact us!